3d printable Rc Plane - 2022


During the summer of 2022, I decided to get involved with learning to fly RC aircraft. Soon after that started, I began designing my own RC aircraft that is fully 3d printable. Over 200 hours were put towards design work as this was my first time designing something with this much detail, Not to mention any sort of RC controlled aircraft/vehicle.
Aircraft Render
Aircraft Render Exploded View
Design Concepts considered beforehand
Aircraft Has to be leightweight
There are 4 main force components that act on an aircraft when in flight - thrust, drag, lift, and gravity. Gravity acts on the aircraft and varies with the weight of the aircraft. In simple terms: the lighter an aircraft, the less thrust/lift required to sustain flight.
I have no experience 3d printing RC aircraft so this concept is still fairly new to me. I somehow have to find a way to design an aircraft of my choosing and make sure the overall weight is as low as possible so that hopefully it can fly.
Reasonable aircraft size
This was something that sounds simple but actually affects a lot of things. I wanted to pick a size that would be able to fit all of the necessary electronics and be able to fight some moderate winds, along with being stable in flight. On the other hand, the aircraft can weigh a lot, and it can't take hundreds of hours to print.
Weight Balance
Having the center of gravity in the right position on an aircraft is key for stable flight. If the CG is too far forward the aircraft will try to pitch down during flight, and if the CG is too far back the aircraft will try to pitch up during flight. Both causing the pilot to add correctional maneuvers, and more drag because of it. Getting the CG in the right place on the aircraft will be key.
Making Print layer Orientation work for me
When printing out a part, you need to take the part orientation into account. Forces will act on parts differently depending on if they are acting parallel or perpendicular to the part. Something I have considered is using carbon rods running perpendicular to the layers to help distribute any strong forces throughout the part(s). This could be particularly useful in the fuselage or the wing.
Another important factor is print Feasibility. One main advantage to 3d printing is that it can produce parts with internal geometry that isn't cheap or possible with conventional engineering manufacturing methods. With that said, the orientation of which you print the part on the printer bed plays a large part on the success of said part. Making sure this is correct beforehand is very important.
Cant Cost a fortune to produce
Having a printer before I thought of this idea is a big cost saver in my project, however there are other things to consider. I need to factor in the cost of the filament, the Carbon rods, all of the aircraft electronics, and a RC remote. I also needed to acquire a park pilot's license. As the size of the aircraft gets larger, I will probably need to use a bigger motor, a bigger ESC, and a larger battery, which all cost more then the previous.


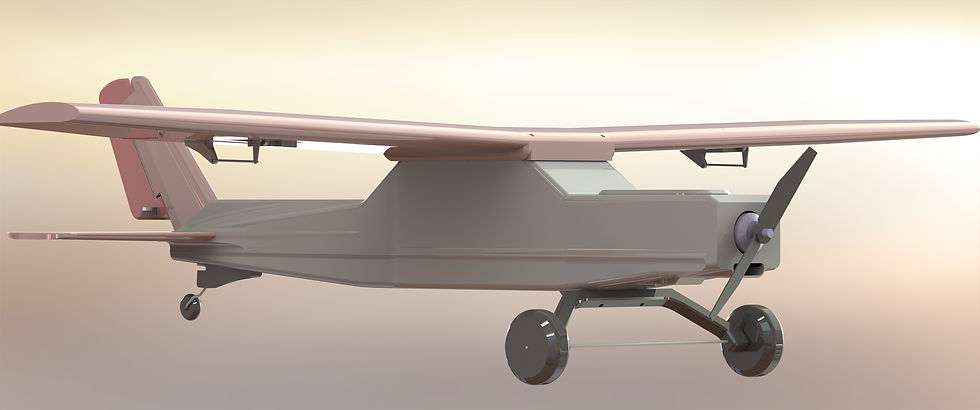



What I learned after designing
Made the walls to thick - long print time
The wing and fuselage wall thickness as stated earlier is 4 layers. This thickness turned out to be too thick - meaning it was too strong and too heavy for what I needed. This led to crazy long print times for the fuselage and wing.
Wing Internal structure was over designed
The internal structure for the wing was over engineered and was also too much for the application. It was very strong but was adding extra print time and weight to the aircraft, both things that I was trying to reduce.
Aircraft was too heavy - Failed expectations
If I really want to get a plane to fly, I need to shave off as much weight as possible going forward. The electronics have added a lot of weight to start out so it's already tough to keep the weight down. One thing I could look into would be printing out my plane in lightweight PLA, or LW-PLA. The Filament acts as a foam as it gets extruded, being less dense than regular PLA, but with similar strength characteristics. Most users report getting parts that weigh 50% less than their counterparts.
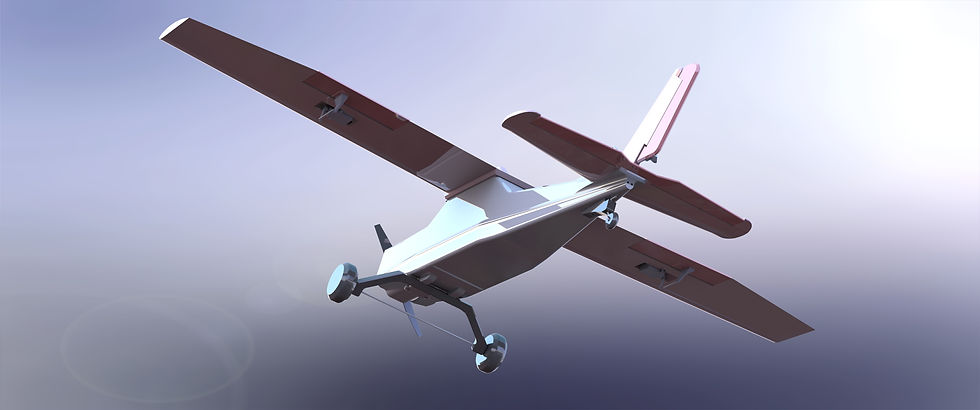

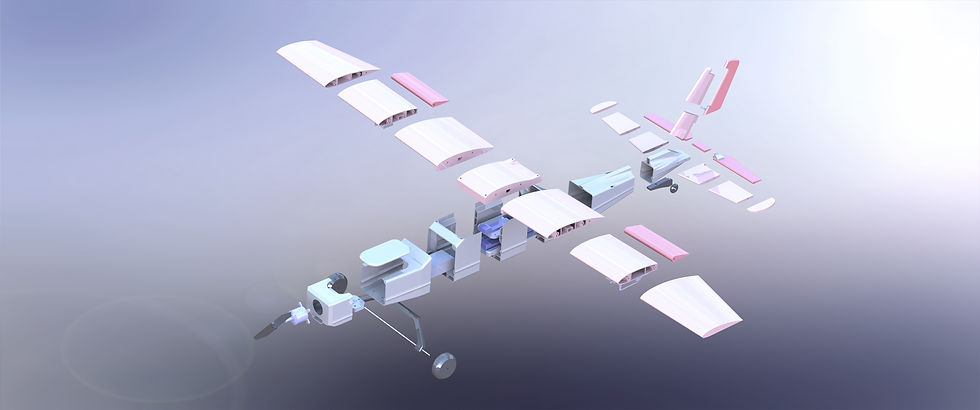



What Would I do Better Next time
Wall Layer Thickness
For the next Design, I plan to try and make the wall thickness 3 or 2 layers. It won't be as strong but I should save a lot of weight and print reduction time from this change. After looking around and seeing that some others print their planes with 2 or 1 layers, i will most likely go with a 2 layer thick wall.
Wing Design
After considering the weight and print time of the entire wing, I realize I need to redesign the wing in a minimalist way if I want to lower the weight. Some options are to decrease the wall thickness, reduce the internal support structure of the wing, and be mindful of the thickness of the wing.
Electronics Unit
This is something that I saw as being difficult from the beginning. I have to have a way to access the battery compartment so I can add/remove the battery. I should be able to adjust the servos from the outside during a mid-flight session. The plane I designed had a removable wing so I have to be able to attach/detach those servo cables. I need to keep the ESC cool so it doesn't melt the PLA frame. The unit needs to house the receiver module and the cables associated with it.



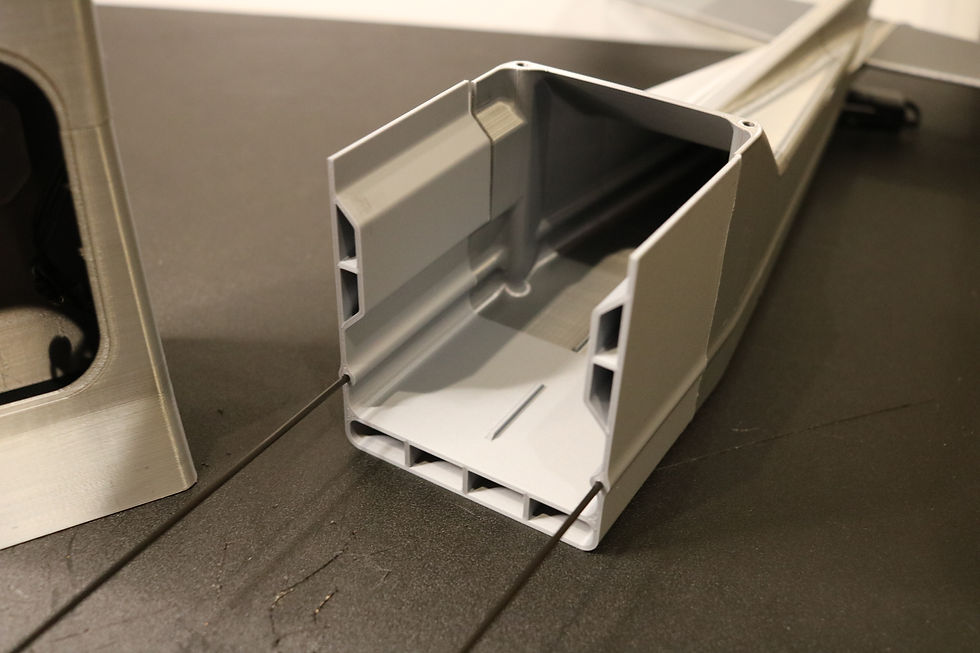


TOTAL PRINT TIME AND WEIGHT
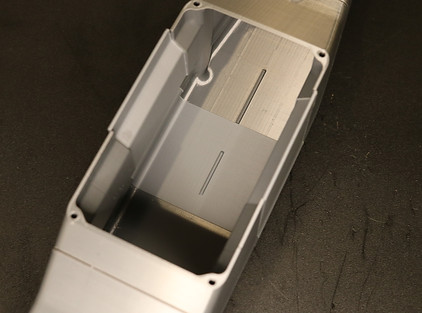
Purchase my 3d printable RC plane here:
_JPG.jpg)